Problem case
Retailers of all sizes are repeatedly struggling with sales losses due to missing or sold out products (so-called “out-of-stocks”). Even with centralized data collection, these problems can only be partially addressed, as a variety of reasons, some of which are difficult to understand, can lead to out-of-stocks. In addition to unexpectedly high sales, theft, breakage (e.g. dropped products) or incorrect data maintenance can also cause empty shelves.
To solve this problem, we have developed a dashboard that can be used to centrally monitor the occurrence of out-of-stocks. Thanks to a variety of analytical functions, individual cases can be found and examined in detail with just a few clicks in order to prevent these incidents in the future. Our tool can be seamlessly integrated into clients' existing dashboard systems and thus offers a low entry threshold for all user groups.
Everyone has experienced it before: You're in the supermarket looking for a favorite product and you end up disappointed in front of an empty shelf. What is annoying enough for us as customers is an even bigger problem for retailers. On the one hand, in the short term, he misses out on several sales (so-called “lost sales”) that would have gone over the counter if the shelves were full. Furthermore, in the long term, retailers can also completely lose customers: Experience shows that customers who have repeatedly been unable to buy their favorite product at a store often change their regular retailer. It is therefore extremely important for retailers to quickly identify such so-called “out-of-stocks” and correct the causes.
So far, however, the analyses of such out-of-stock have largely been carried out without specific support, but only with the general tools of the respective ERP system (enterprise resource planning). In doing so, employees must manually identify the dependencies and causes of the problem, often based on years of experience. However, this is problematic in many ways: On the one hand, the causes of out-of-stock can lie in all areas of the company and in its complex supply chains (e.g. warehousing, suppliers), and on the other hand, many unforeseeable events such as theft or breakage can influence the product inventory. As a result, the manual search for causes is time-consuming and prone to errors.
Out of Stock Dashboard as a solution
That's where we start and, with our out-of-stock dashboard, offer a visualization and analysis tool that offers the best possible support in finding and resolving out-of-stock problems, tailored to the problem.
To achieve this, our dashboard offers individualized views for every level of the company: Whether at the branch, at regional level or across Germany, users can classify and analyze out-of-stock cases in their area. The central overview, which can be seen in [Figure 1], is always structured in the same way: In the upper section, you can view the branches, products, product groups and suppliers that currently have the highest out-of-stock rates - arranged in color and expressed as percentages. In the lower area, again, various graphics show.
- How sales and lost sales developed in absolute terms over the last week.
- How the out-of-stock rate of the current selection has developed compared to the total quantity in the last week.
- How out-of-stock cases are distributed across the various regions. The size shows the absolute number of cases, the color in turn shows the percentage of the total portfolio (out-of-stock rate).
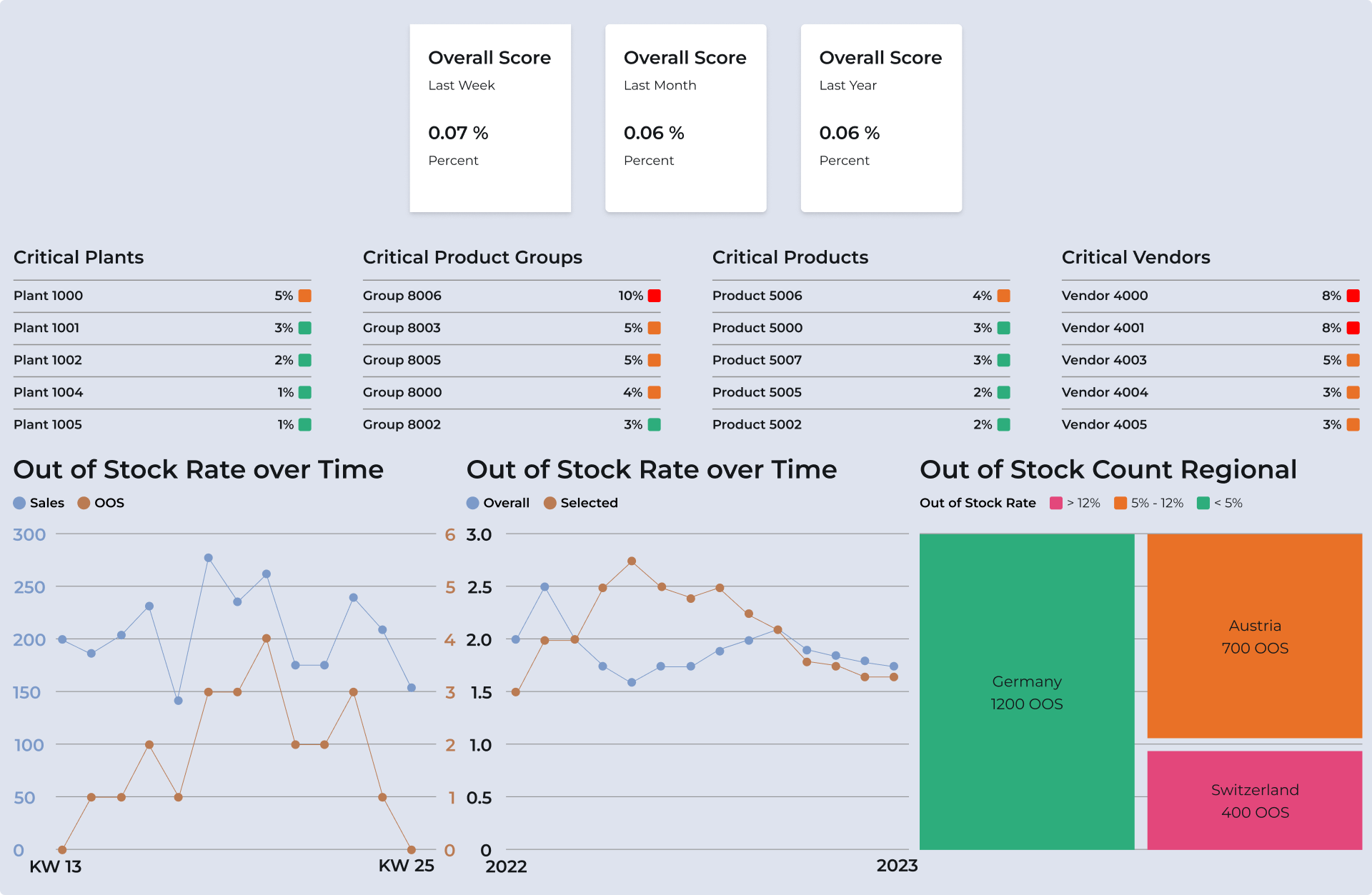
Each element in the dashboard, both at the top and bottom, can be used to filter the data for appropriate selections. In this way, it is possible to increase the level of detail from the initial overview down to the level of an individual OOS case. Example: You select a particularly eye-catching supplier at the top right of the overview. You can then select a region to view at the bottom right of the tree map chart (3). With the help of a “drill-down”, you can navigate one level lower and then view all branches in the region. With another “drill drown”, you in turn achieve out-of-stock cases for all products from a selected branch, which of course continue to be filtered on the originally selected supplier. With the help of a final “drill down”, you finally reach the detailed view [Figure 2], which allows you to view a specific out-of-stock case, i.e. a product in a branch.
The detailed view offers 3 components: General facts are listed at the top left, and at the bottom you can see the statistics for this product-store combination over time. It gets particularly interesting at the top right: Based on past data, our dashboard provides a prediction of which reasons and are likely to have contributed to the current out-of-stock, thus saving unnecessary searches in the wrong direction.
Our solution is directly integrated into the customer's ERP systems. This offers two decisive advantages: On the one hand, we minimize interfaces and the dashboard is always up to date with all goods movements. On the other hand, this makes it easier for users to get started, as our out-of-stock dashboard fits seamlessly into the users' familiar environment.
Conclusion
Our out-of-stock dashboard provides a central point of contact for analysing out-of-stock situations of all types in retail in a targeted and efficient manner. Starting with a general overview, you can work your way down various paths down to individual cases. There, predicting the tool helps to further narrow down the possible reasons. This forms the basis for subsequently preventing future out-of-stock cases with the right measures and thus increasing sales and customer loyalty in the long term.